3 Wire Form Design Considerations that Reduce Manufacturing Costs
Many of us have taken an economics class and have learned about the law of supply and demand. In case you missed that class, here is a great definition of supply and demand from Investopedia:
“The law of supply and demand combines two fundamental economic principles describing how changes in the price of a resource, commodity, or product affect its supply and demand.
As the price increases, supply rises while demand declines. Conversely, as the price drops supply constricts while demand grows.”
Every business is affected by the law of supply and demand. If you have to increase the price of your product then your demand might decrease which means you may be forced to lower your prices. So it is important to sell your products at a price your customers are willing to pay. Here are 3 tips on how to lower your wire form manufacturing costs.
1. Use a common wire form material
It’s important to use a wire form material that allows you to provide your customers with good quality products. With that being said, you also want to provide your customers with products at a price they are willing to pay. We could go into cost details of different materials that we use for wire forms and what is the most effective for your product but there are many varieties and of course prices change.
The best way to cut material costs is to select a common material that is readily available. For example, don’t ask for a wire form material that has a “platinum” price tag because it’s scarce. Be prepared to ask the wire form manufacturer the right questions about cost-effective wire form materials. To learn more about some of the wire form materials commonly use, read our blog “Get Wired With This Guide To Wire Forming Steel!”.
2. Limit each wire form component to a maximum of 8 bends
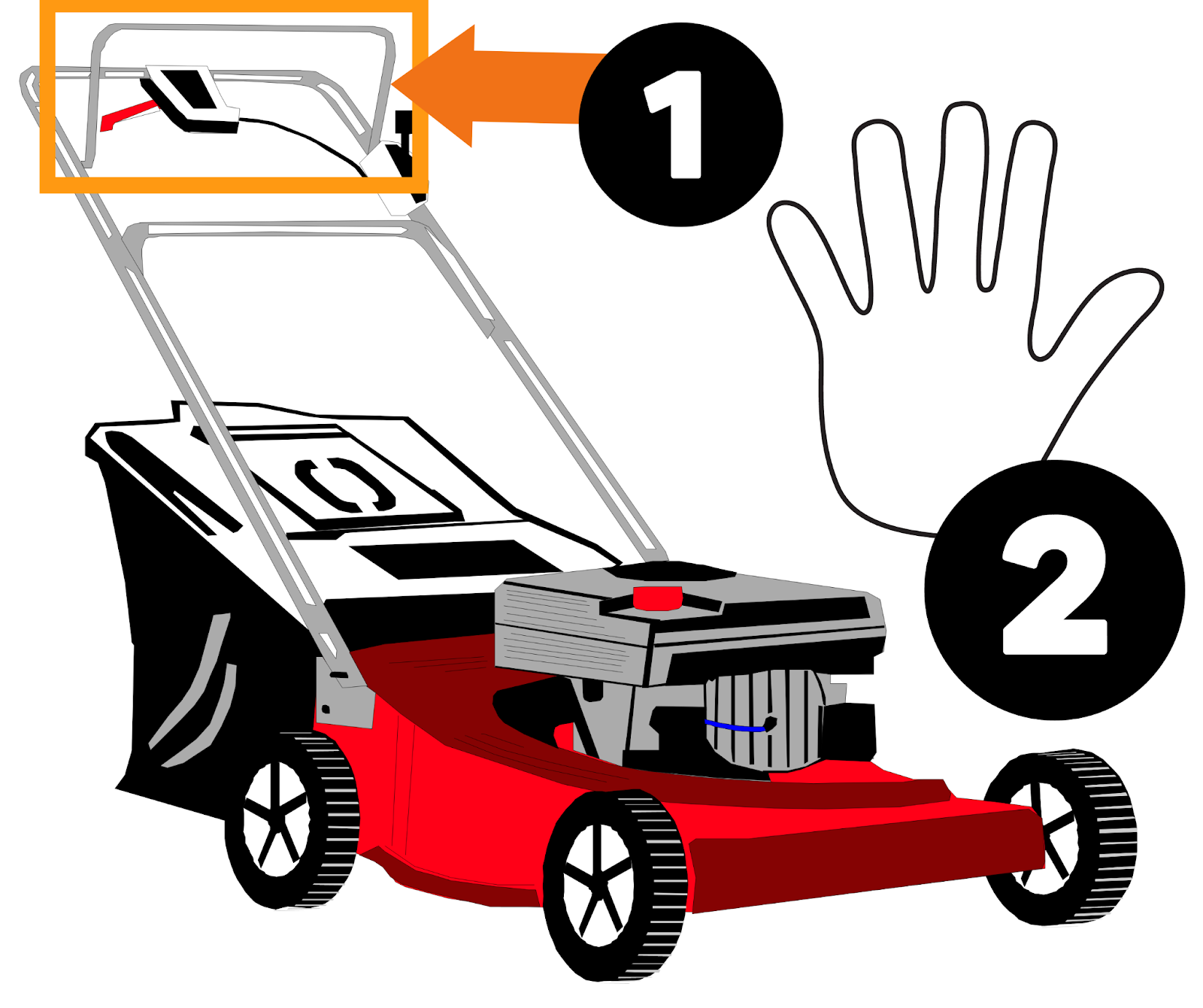
You might not have considered that bends in a wire form come at a cost. Each bend slows down the production process. The more bends, the more hours that are needed to create the wire form. Look at the image we have provided of the lawnmower (focus on the safety on/off lever in the orange box ) and the outline of the hand. Do you think a wire form of the safety lever, with around 4 bends is more or less complicated to create than the outline of the hand that has around 15 or more bends? The hand would take up more time because it is a more complex wireframe therefore it costs more.
3. Make sure the bends in your wire form are not too close together
Let’s go back to the image of the outline of the hand, each finger curve involves bends that are very close together, especially between the middle finger and the ring finger. The closeness of the bends and the number of bends make this a very time-consuming and complicated wire form to produce, especially with very large order quantities that slow down a good portion of the whole manufacturing facility.
There are other cost variables that could affect the manufacturing costs of your wire form which could include the final coating of the product, the proximity of the wire form manufacturer from your manufacturing facility, and more. If you are looking to lower the costs of your wire form, consider one of these three tips and discuss cost-effective changes to your design without sacrificing quality with a wire form manufacturer representative.
WireTech Tip!
If you’re looking for more “bends” in your life, then try yoga!
Stay updated On Wiretech
Address
124 E Leeward Street
Sturgeon Bay, WI 54235
General inquiries
OFFICE 920-743-7201
careers@wiretechfab.com